18 Apr A penetrating gaze: System allows world’s first X-ray look at electron-beam 3D-printing process
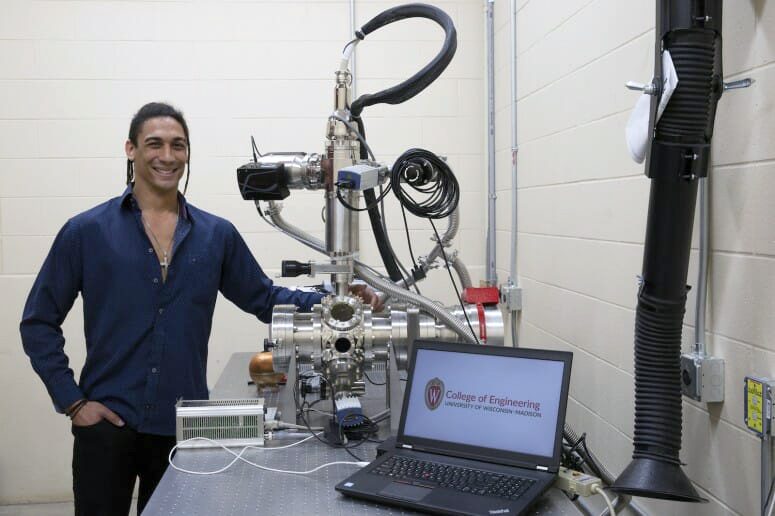
Graduate student Luis Izet Escano with the apparatus he developed to study the structure of metal parts manufactured with a cutting-edge 3D printing process. PHOTO COURTESY IZET ESCANO
Combining special, high-energy X-rays with thermal imaging and visible light, engineers at the University of Wisconsin–Madison are looking inside metal items made with a new 3D-printing technique to better understand (and eventually refine) the promising manufacturing method.
Building geometrically complex or one-of-a-kind designs — artificial joints designed from a scan of the original human bone, for example, or strong, lightweight components for rovers sent to other planets — are among the applications for a 3D-printing process with metals called electron beam powder bed fusion.
“For electron beam powder bed fusion, right now, there’s pretty fast growth,” says Lianyi Chen, an assistant professor of mechanical engineering at UW–Madison. “It’s an important technology to make parts for aerospace—for example, for jet engines, with titanium aluminide. We can’t make these with any other 3D-printing technology.”
Electron beam powder bed fusion begins with a base of metal powder on a substrate. An electron beam melts and fuses additional powder layers to construct a part from the bottom up. While the process sounds straightforward, it’s new enough to be less than well understood. There are lots of physical phenomena at play, and defects hidden within metal layers could cause failures without warning.