15 Mar Dramatically reducing defects, new technique opens applications for 3D-printing metal parts
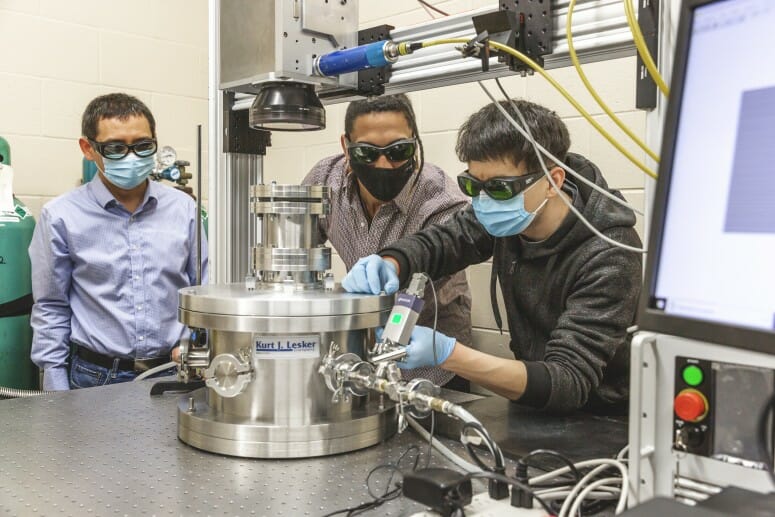
UW–Madison mechanical engineering professor Lianyi Chen, left, and doctoral students Luis Escano and Minglei Qu, right, work in Chen’s lab, where they developed a technique to limit defects in 3D printing with metals. UW–MADISON PHOTO BY RENEE MEILLER.
Compared to conventional manufacturing methods, additive manufacturing (also known as 3D printing) is far better at producing metal parts with very complex shapes, making 3D printing attractive for applications in aerospace and biomedical industries, among others.
But there’s a downside. Metal parts created with additive manufacturing have defects, such as pores and cracks in the material, that significantly compromise the finished part’s strength and durability.
“Using metal 3D printing, we haven’t been able to consistently produce parts with the same high quality and reliability as those made by conventional methods, which means we have big concerns about using 3D-printed parts for critical or load-bearing applications where failure isn’t an option,” says Lianyi Chen, a University of Wisconsin–Madison assistant professor of mechanical engineering. “This quality problem is the biggest barrier for using metal 3D printing in various applications.”
Now, Chen and his students have discovered a way to enable a prominent additive manufacturing technique called laser powder bed fusion to produce metal parts that have significantly fewer defects. They detailed their findings in a paper published recently in the journal Nature Communications.
“We demonstrate a potential way to solve the quality problem by making metal 3D printing technology much more reliable, enabling it to produce consistent, defect-lean parts,” Chen says. “Using our unique method, we were able to 3D print a metal part that has very few defects and a comparable quality to that of a commercially manufactured part that you could buy off the shelf.”